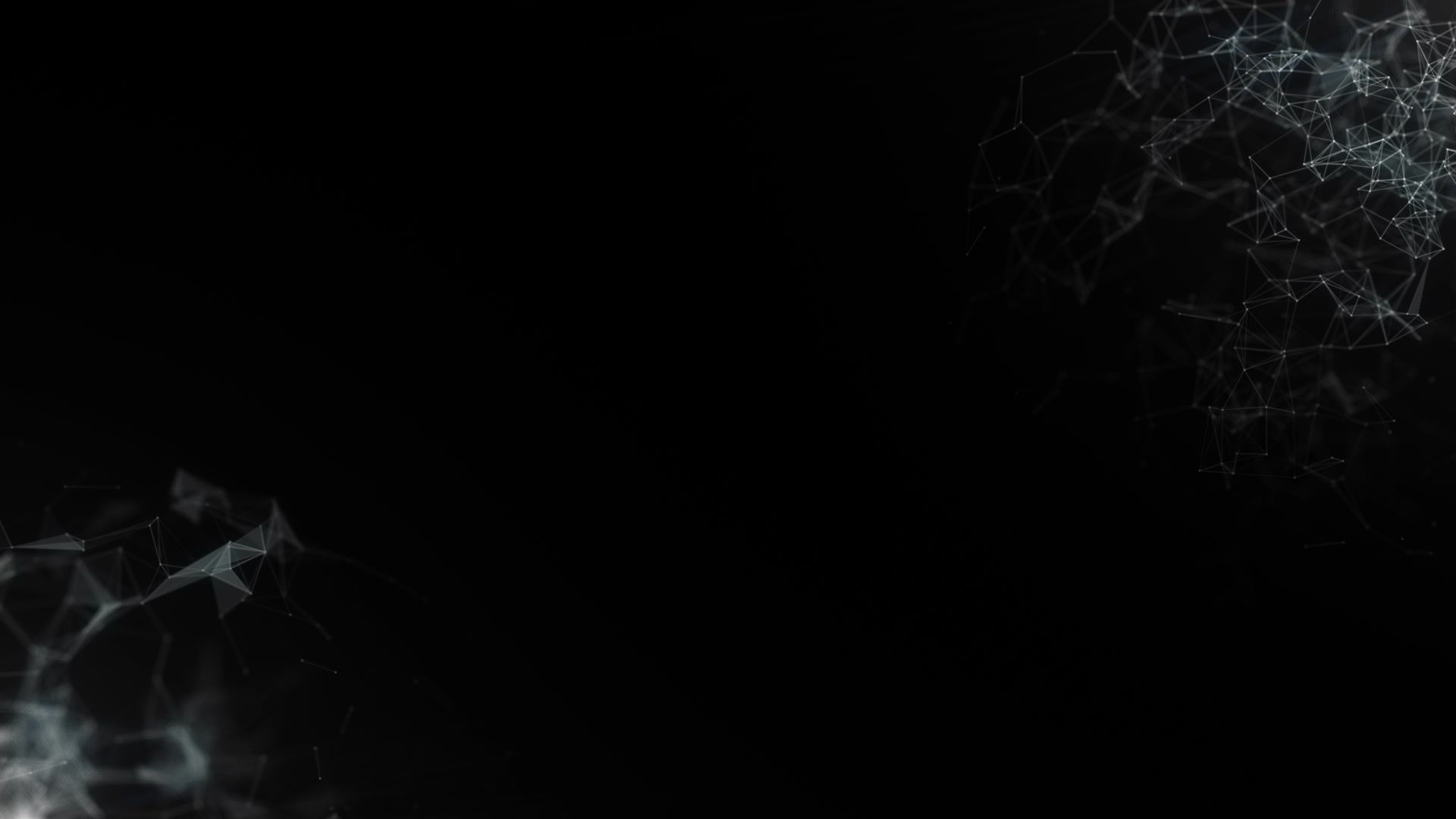
ACUSTIC MIXSERS
ACUSTIC MIXSERS
ÇİFT VİDALI EXTRUDER SİSTEMLERİ
ÇİFT VİDALI EXTRUDER SİSTEMLERİ
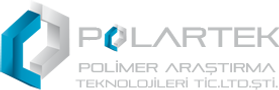
Nearly Perfect Machines
Search Results
20 items found for ""
- PILOT INJECTION | POLARTEK POLIMER
PILOT LINE INJECTION BOY 35 E The BOY 35 E is a four-tie bar, fully hydraulic reciprocating screw injection moulding machine with two-platen clamping unit and swivel-out injection unit. BOY 50 E As entry-level model with 500 kN clamping force, the BOY 50 E includes a multitude of functions already in standard execution. BOY 60 E With its appealing design, the BOY 60 E is an optical highlight. But it is more than just optics which convinces the experts, namely its technical and operational values and its orientation towards cost-saving.
- Extruder Extrusion| Polartek Poli̇mer Araştirma Teknoloji̇leri̇ Ti̇c.ltd.şti̇. | İstanbul
WHAT WE DO EXTRUSION EXTRUSION LAB INJECTION LAB INJECTION Bi-Tri Component Melt Spinning Line Bi-Tri Component Melt Spinning Line NON WOWEN NON WOWEN ACOUSTIC MIXSER RESONANT MIKSER 3D FILAMENT LINE 3D FILAMENT LINE SPECIAL MACHINE SPECIAL MACHINE ULTRA SILENT DRY AIR COMPRESSOR ULTRA SILENT DRY AIR COMPRESSOR GAS SOLUTIONS LAB GAS LINE We are manufacturer and supplier of Extruder Systems , Injection Moulding Machine and Acoustic Mixers, We manufactured and sold many extruders to food, textile, polymers, academia etc. In Turkey and to many countries. We are supplier of high performance equipment for the manufacture of technical materials. We are able to supply a variety of systems in laboratory, pilot, and production scales for polymers, foods, pharma, and defence. We are distributor of FET, Fibre Extrusion Technology, is a leading supplier of state of the art process technology and equipment for the man-made yarns and fibre extrusion industry. FET offers in-depth expertise and knowhow into design, process technology, electronics, manufacturing and after sales service. FET support customers for developing of new products and for R&D departments for man-made fibre and yarn extrusion. We are represent one of leading company, BOY, for injection moulding machine. BOY injection moulding machines: Innovation in plastic processing Impressiv advantages: BOY's design concepts are; Maximum flexibility, Small footprint, Optimum production conditions, Large mould fixing dimensions, Flexible use of moulds, Intuitive use of control, Comfortable operation, Minimum electricity consumption, Low cooling capacity ,
- Bi & Tri COMPONENT MELT SPIN |Polartek Poli̇mer Araştirma Teknoloji̇leri̇ | İstanbu
Bi & Tri – COMPONENT MELT SPINING TECHNOLOGY FET-100 Extrusion Central to all FET laboratory and pilot melt spinning systems is the specially developed extrusion module, the FET-100 Extrusion which allows multiple process options. This extrusion module is designed to provide melt spinning capacity to any one of the three downstream process options. The module is mounted on a hydraulic lifting table which permits automated adjustment of the working height. FET-101 Multifilament FET offers a wide range of bespoke pilot and laboratory melt spinning systems for continuous multifilament applications capable of matching the demands of all users. Each variation of the FET-101 Multifilament option is uniquely specified and designed for world leading companies and research institutes for a wide variety of applications. FET-102 Nonwoven Simple integration of the FET-102 Nonwoven option gives the possibility of melt spinning nonwoven materials. Melt blown and spun bond types can both be achieved on the same base system. This is applicable to a broad range of polymers, including viscous materials normally not appropriate for the melt blowing or spun bond process. Applications include resorbable biomedical polymers and engineering grade materials. FET-103 Monofilament Utilising the same extrusion module, FET can also provide specialist laboratory and pilot melt spinning systems for monofilament applications, the FET-100 monofilament. As with multifilament equipment, our flexible monofilament systems are being used by high tech organisations and research institutes on a variety of technical and R&D projects. BI-COMPONENT & TRI- COMPONENT MELT SPINNING MULTI-FUNCTIONAL LABORATORY & PILOT MELT SPINNING SYSTEMS FET-100 Extrusion FET-101 Multifilament FET-102 Nonwoven FET-103 Monofilament A significant development is that FET-100 systems can be specified to be multi-functional, allowing for easy and fast conversion between material formats. It configures to all combinations of multifilament, monofilament and melt spinning of nonwoven structures as required. This highly versatile and flexible system is ideal for research and development, designed specifically for detailed investigation into extruded textile materials. Benefits include substantial savings on cost, floor space and also the ability to add optional equipment in the future. “High Capability, Multifunctional, Cost-Effective and Flexible” Multi-Polymer and Multiple Format Capability MELT SPINNING SYSTEMS FOR NON-WOVEN STRUCTURES DEVELOPMENTS IN THE MANUFACTURE OF NON-WOVENS As a result of innovative development work by FET, non-woven structures can now be readily made from “difficult to process” polymers. The new processing technology is a unique adaptation of the melt blowing process and makes possible the conversion of a wide range of polymers into non-woven webs, using a single processing stage. For many of our clients, the benefits of single stage manufacturing and the flexibility provided solve many processing problems and give them a substantial competitive edge. Process applications New process have been developed in particular for polymers that have properties which would in normal circumstances make them unsuitable for melt blowing, such as high melt viscosity or susceptibility to degradation. These versatile systems enable the extrusion of melt blown nonwovens with a broad span of structures and mechanical properties, such as: Those required for filtration applications Bio-medical applications using resorbable polymers Structures which exploit polymer properties such as thermal and chemical resistance Along with: Simpler processing route than other techniques such as needle felts There are numerous options for post processing of the web, by calendaring, point bonding or lamination Equipment for melt spun fibres and yarns can be tailored to precise client requirements and are also available for small batch production, pilot and laboratory applications. WET SPINNING LINE FET 200 SERIES LABORATORY SCALE WET SPINNING SYSTEMS INTRODUCING THE FET-200 LAB In addition to pilot and small scale wet spinning production lines, FET now also designs and manufactures a lab scale version which is more suitable for the early stages of formulation and process development. Systems can be supplied for a wide range of different fibre types. These have ranged from corrosive aqueous salt solutions (such as alginate fibres), to acidic systems (such as engineered silk) and also systems using flammable, toxic solvents (such as UHMWPE). The FET-200 LAB system is ideal for formulation and process development: Compact design makes efficient use of laboratory space whilst delivering high level of functionality Enables accurate replication of processes on a small scale Allows full exploration of processes with low volumes of processing solutions Capable of processing wide range of materials: e.g. corrosive, flammable, acidic FET-200 FEATURES Dope tanks from 1 Litre working volume General Purpose unit is temperature controlled with electrical heater and has variable speed impeller Options for cooling jackets and alternative impeller designs Many other impeller options including helical and ribbon designs Accurate flow to spinneret via speed-controlled gear pump Numerous interchangeable options for spin heads, including submerged Coagulation tanks with recirculation Wash tanks with multiple pass options Filament drying systems Filament orientation systems Take-up winding solutions Computerised control system with data capture and recording
- BİG TYPE INJECTION | POLARTEK POLIMER
BIG LINE INJECTION BOY 80 E The BOY 80 E provides 800 kN clamping force. Given the easy handling of the machine, the users of the BOY 80 E enjoy maximum flexibility. BOY 100 E Some more of everything! Greater daylight between tie bars and larger platen distances as well as a clamping force of 1000 kN characterize the BOY 100 E. BOY 125 E Significantly stronger, larger and more powerful, were the requirements for the development of BOY 125 E. 1,250 kN clamping force characterizes now the new machine upper limit at BOY.
- LAB INJECTION | POLARTEK POLIMER
LAB INJECTION BOY XXS The flexible BOY XXS proves its advantages especially in the production of prototypes, in small series, e.g. in the production of spare parts and in the manufacture of micro to small parts. BOY XS The BOY XS is a development from BOY – an injection moulding machine designed with well-proven technology and all the merits of our larger machines. BOY 22 A PRO The BOY XS is a development from BOY – an injection moulding machine designed with well-proven technology and all the merits of our larger machines.
- Special Extrusion | Polartek Poli̇mer Araştirma Teknoloji̇leri̇ | İstanbul
SPECIAL EXTRUSIONS Lab Small Multi Layer Cast Film Machine | 2 layer| 3 layer | 5 layer Cast Film Test Line Lab small multi layer cast film machine | 2 layer| 3 layer | 5 layer cast film test line FEATURES The user can select the number of small lab extruder according to the structure of the film, and combine with the double layer cast film die, three layer cast film die or five layer cast film die to form a small lab multi-layer co-extruded blown film machine. The film structure design can be divided into A/B, A/B/C, A/B/C/B/A, A/B/C/B/A, A/B/C/D/E symmetrical or asymmetric structure according to the die and numbers of small extruder. Molds can be made with an Feed Blocks or Multilayer Manifold Dies. The Feed Blocks die has a lower price, which can meet the need of sample making in conventional laboratory products. The Multilayer Manifold Dies can meet the application of higher thickness uniformity and higher layer ratio. The lab mini extruder is driven by servo motor, controlled by PLC, PID temperature setting, screw structure optimization to ensure good plasticization and stable extrusion. The roller can be manually lifted and lowered to reduce the air gap between the Die, to improve the film quality. Hard chromium - plated mirror roller with 304 stainless steel roll core, reliable quality, highly surface finish for product. The machine all driven by servo motor, to achieve smooth and precise running. Each roll of the lab small multi-layer coextruder is driven independently by servo motor, and the running is stable. The speed ratio of each roll can be adjusted freely. Advanced multi-axis synchronous technology ensures the synchronization of each roll speed. Advanced PLC control and mobile touch screen operation ensure system stability and improve operation convenience. Gravimetric feeder is optional. Melt pump is optional. On this basis, it can be derived into lab small multi-layer co-extrusion calender machine and lab small multi-layer co-extrusion film laminating machine. MDO longitudinal stretching unit can be selected to form lab small online cast film MDO stretching line. Lab Multi Layer Blown Film Line 2 Layer, 3 Layer, 5 Layer Film Blowing Machine Lab Multi Layer Blown Film Line 2 Layer, 3 Layer, 5 Layer Film Blowing Machine FEATURES The user can select the number of small lab extruder according to the structure of the multi layer blown film, and cooperate with the 2 layer blown film die, three layer blown film die or five layer blown film die to form a small lab multi-layer film blowing machine. The film structure design can be divided into A/B, A/B/C, A/B/C/B/A, A/B/C/B/A, A/B/C/D/E symmetrical or asymmetric structure according to the die and numbers of small extruder. The multi layer blown film die includes sleeve type, planar superposition type, subuliform superposition type etc. Among them, planar superposition die is suitable for materials with large temperature difference and sensitive to temperature because it can be divided into sections for temperature control. The lab small extruder is driven by servo motor, controlled by PLC, PID temperature setting, screw structure optimization to ensure good plasticization and stable extrusion. Motorized height adjustment film tower, convenient to lead film and process adjustment. Hard chromium - plated mirror roller with 304 stainless steel roll core, reliable quality, highly surface finish for product. Film bubble stabilizing cage and synchronous adjustable film collapsing frames with polished teak wood or guide roller. The machine all driven by servo motor, to achieve smooth and precise running. Each roll of the lab small multi-layer blown film line is driven independently by servo motor, and the running is stable. The speed ratio of each roll can be adjusted freely. Advanced multi-axis synchronous technology ensures the synchronization of each roll speed. Advanced PLC control and mobile touch screen operation ensure system stability and improve operation convenience. Gravimetric feeder is optional. Melt pump is optional. Refering: Lab small multi layer blown film line, small multi layer film blowing line, lab multi layer co extrusion film blowing machine, small multi layer co extrusion blown film machine. Mini Type Multi Layer Co-extrusion Casting & MDO Film Line Mini Type Multi Layer Co-extrusion Casting & MDO Film Line FEATURES Both extruders are controlled by the main touch screen controller for remote control. Preparation of single or multi layer casting film. Preparation of coating film. Preparation of machine direction orientor(MDO) with multilayer co-extrusion cast film. Optional melt pump and static mixer can improve plasticization and film quality. Optional Mold Temperature Controller and Water Cooling device is available for temperature control. Optional air knife or electrostatic adsorption device can improve the film adsorption & cooling. Optional waste film trimming collection device improves winding quality. Optional constant tension winding device producesf smooth film and high quality. Optional pattern roller/matte roller can be used for different surface treatments. Feature and size is customizable. A PPLICATIONS Preparation of multilayer functional film. Polymer casting performance test. Polymer MDO performance test. New formula development. Optimization of processing parameters. Small scale preparation of narrow film. Laboratory Multi Layer Co-extrusion Coating & Casting & Laminating & MDO Line Laboratory Multi Layer Co-extrusion Coating & Casting & Laminating & MDO Line FEATURES Both extruders are controlled by the main touch screen controllerfor remote control. Preparation of single layer cast film. Preparation of multilayer co-extrusion cast film. Preparation of machine direction orientor(MDO) with multilayer co-extrusion cast film. Optional melt pump and static mixer can improve plasticization and film quality. Optional Mold Temperature Controller and Water Cooling device is available for temperature control. Optional air knife or electrostatic adsorption device can improve the film adsorption & cooling. Optional waste trimming collection device improves winding quality. Optional constant tension winding device producesf smooth film and high quality. Optional pattern roller/matte roller can be used for different surface treatments. Feature and size is customizable. APPLICATIONS Preparation of multilayer functional film. Polymer casting performance test. Polymer MDO performance test. New formula development. Optimization of processing parameters. Small scale preparation of narrow film. Biaxially Oriented Film Stretching Machine-Biaxial Stretching Film Simulator Biaxially Oriented Film Stretching Machine-Biaxial Stretching Film Simulator FEATURES Including biaxial stretching mechanism, static pressure box, heating oven High-performance temperature sensor Servo motor drive Real-time monitoring of polymer materials, tensile changes in the film APPLICATIONS Prepare Biaxially oriented film samples for properties test and optimization of formulations. Evaluate the biaxial orientation capability of new materials and films in lab-scale. Biaxial tensile properties of polymer film. Investigate biaxial orientation temperatures, ratios, speeds for production scale up. Two Roll Calendering Laminating Line Two Roll Calendering Laminating Line FEATURES The rollers are independently driven by servo motorsfor flexible speed control. Chrome coated mirror roller with 304 stainless steel shaft guarantees reliable quality and excellent film appearance. Roller's number is optional, 2/3/4/5 rollers are acceptable. Optional Mold Temperature Controller and Water Cooling makea uniform temperature distribution on roll surface. Optional trimming waste collection device improves sheet quality. Optional constant tension winding device producessmooth film and high quality. Optional pattern/matte roller can be used for different surface treatments. Optional hydraulic or air cylinder for different materials. Optional two / three / four rollers configurationfor different processing technology. APPLICATIONS Calendering and laminating is available Preparation of different sheet. New formula development. High viscosity polymer calendaring. Preparation ofmulti-functional polymer composite sheet. Rubber Extrusion Calendering & Laminating Line Rubber Extrusion Calendering & Laminating Line FEATURES Each roller is independently driven by servo motor, ensuring precise roller revolution speed and speed ratio between adjacent rollers. Chrome coated and mirror polished roller with 304 stainless steel shaft guarantees reliable quality and high surface quality of film. Optional melt pump and static mixer can improve plasticization effect and film homogenization. Optional Mold Temperature Controller and Water Cooling device. Optional trimming collection device improves winding quality. Optional Constant Tension Device makes smooth winding effect and steady subsequent machine direction tensile. APPLICATIONS Preparation of different sheet. New formula development. High viscosity polymer calendaring. Preparation ofmulti-functional polymer composite sheet. Machine Direction Orientor MDO Machine Pilot Line Machine Direction Orientor MDO Machine Pilot Line FEATURES The horizontal structure is easy to expand and convenient to thread the film, more suitable for pilot and small-scale production. Preheat roller, stretching roller, annealing roller and cooling roller are independently driven by servo motor, with higher speed control accuracy. Stretch roller gap adjustable, can achieve "zero pitch" stretch, reduce necking effect. Single, double (or even multi-point) stretch optional, adjustable stretch ratio. Oil / electric heating optional: oil heating. Temperature uniformity, and electric heating can obtain higher process temperature. High-performance PLC with 10-inch touch screen, high control accuracy, more convenient operation. Horizontal or vertical configuration optional APPLICATIONS Machine Direction tensile membrane laboratory preparation and pilot-scale production. Study and optimization of machine direction stretching production process. Tensile testing of films. R&D of new film materials and ln-line machine direction stretching combined with extrusion casting test lines. Machine Direction Orientor MDO Machine Machine Direction Orientor MDO Machine FEATURES MDO machine can use as an offline stretching film machine, or combined with small single screw extruder, small twin screw extruder, small triple screw extruder, and a small cast film machine, to form a MDO on-line cast film stretching machine. Or you can choose the MDO casting integrated machine. Rollers for preheating, stretching, annealing and cooling are all independently driven by servo motors. The gaps between the rollers can be adjustedby moving the relevant roll horizontally. Mold Temperature Controller and heat conduction oil is adopted to heat the rollers. 10’ touch screen controlleris easy to operate. European standard aluminum alloy frame makes it light, strong, corrosion resistant and durable. 304 stainless steel desktop, practical and beautiful. Single or multi stage draw sections. Size customizable APPLICATIONS Off-line film machine directionorientation. Optional single-point or two-point machine direction orientation. Combined with Mini Precise Film Casting Line an on-line MDO line is made up. Preparation ofstretching film with different draw ratio. New formula development. Functional film preparation and processing research. Filmtensile performance test. Optimization of film stretching parameters. Triple Screw Die Face Cutting Triple Screw Die Face Cutting Granulation Line Use For Ceramic Phone Backboard FEATURES In order to meet the application requirements of the high fill ratio of zirconia ceramics, the triple screw die face cutting granulation line is specially upgraded as follows Triple screw extruder has better dispersing effect and staying time than twin screw extruder and is especially suitable for the blending extrusion of high filling master batch. In order to meet the application demand of high filling zirconia ceramic powder, the extruder adopts ultra-high torque drive system The optimized combination of screw elements can improve the plasticization and homogenization effect and ensure the high fluidity of filling inorganic material Both the screw element and the barrel lining are made of imported advanced alloy steel, and the wear resistance is improved significantly, which is half of the time than common steel. Specially optimized heating and cooling system ensures material temperature control and product performance Driven by a high power motor, the cutting head provides strong power and is equipped with a strong and sharp cutting tool, which is especially suitable for hard ceramic particles PPTC Resettable Fuse Sheet Extrusion Line PPTC Resettable Fuse Sheet Extrusion Line FEATURES The rollers are independently driven by servo motor, sfor flexible speed control. Chrome coated mirror roller with 304 stainless steel shaft guarantees reliable quality and excellent film appearance. The roller are specially strengthened to cope with the high hardness of the sheet. APPLICATIONS This euqipment is made for PPTC resettable fuse sheet. Preparation of different sheet, and laminating sheet, as ABA/ABC structures. New formula development & pilot manufacture. High high filler polymer calendaring. Preparation of multi-functional polymer composite sheet. Filter Pressure Value (FPV) Tester Filter Pressure Value (FPV) Tester FEATURES The melt pump is driven by servo motor. Equipped with manual plate nitride treated screen changer of high hardness and wear resistance. High precise melt pressure sensor provides an accurate melt pressure. The extruder can be moved axially along the linear guide rail on the top of the frame. APPLICATIONS Accurate measurement of melt volume flow rate. Accurate melt conveying. Accurate pressure measurement before and after the melt pump Masterbatch dispersion test. Quality inspection and control during film production. Pigment quality inspection and control. Torque Rheometer Torque Rheometer FUNCTION It provides power for other modules to extract data from temperature, pressure and torque, and then calculates and graphically. It can connect torque module, capillary module, single/twin/triple screw extruder module, casting module, calendering module etc.. FEATURES Driven by high precision servo motor. Controlled by advanced OPC technology and manipulated viaan independent computer. Remote/local multi-point control is available for each independent unit. Labview® based data analysis program with powerful functions and user-friendly interface. APPLICATIONS Operation and control platform forpolymer rheo-station to control other modules. Providedriving, measurement and control function for the other modules.
- News (All) | POLARTEK POLIMER
INJECTION sdfgsdfgsdfgsdfg
- News
INJECTION sdfgsdfgsdfgsdfg