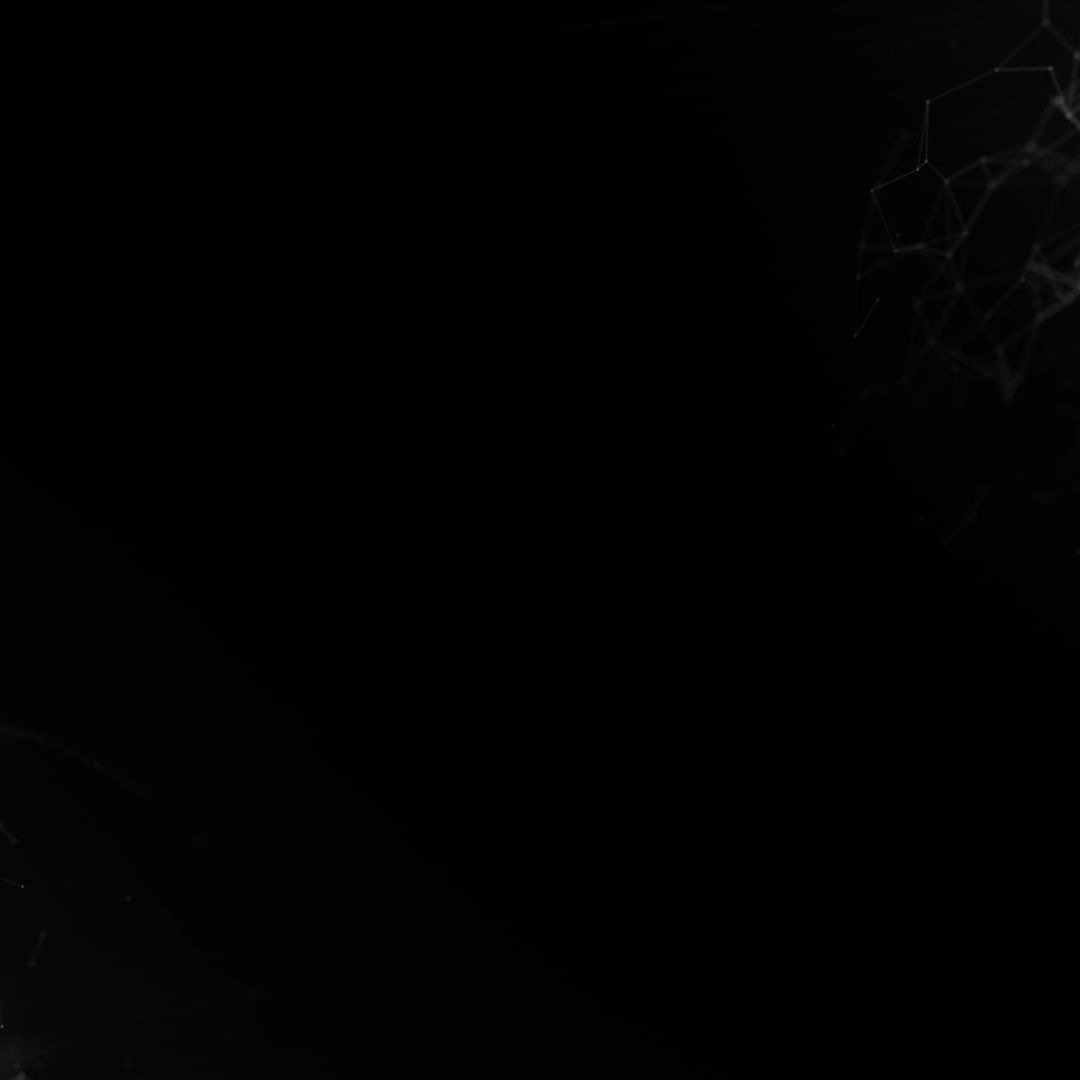
AKUSTİK MİKSERLER
AKUSTİK MİKSERLER
ÇİFT VİDALI EKSTRUDER SİSTEMLERİ
ÇİFT VİDALI EKSTRUDER SİSTEMLERİ
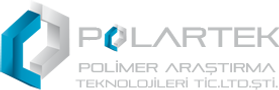
Neredeyse Mükemmel Makineler
Arama Sonuçları
21 results found with an empty search
- 3D Pellet Printer| Polartek Polimer Araştirma Teknoloji̇leri̇ | İstanbul
3D Pellet Printer, 3D Granule Printer, 3D filament, 3D Printer,3D Filament line INDUSTRIAL PELLET 3D PRINTER G5Ultra Pellet 3D Printer Desktop, Built Volume: 500×500×400mm The G5Ultra Pellet 3D Printer utilizes cost-effective thermoplastic pellet feedstocks, ensuring high-speed production. Key features include a nozzle temperature of up to 420℃, rapid hot bed heating to 120℃, and a screw extruder design, accommodating a wider range of materials. Designed to cater to the demanding needs of educational and academic research, design studios, prototyping and more. Get a quote Nozzle Temperature up to 420℃ The next generation extruder (with segmented heat zones) can fit nozzles in diameters ranging from 0.4mm up to 3mm, and the machine can print pellets/granules measuring 2-5mm in diameter. The particles are fed into the extruder from a 3 liter hopper, ensuring a ready supply of feedstock for its huge deposition rate. It heats up to a toasty 420°C, enabling the printing of a wide range of materials. Intelligent Laser Ranging Using laser sensor non-contact measurement technology, the leveling time can be significantly shortened and the leveling accuracy can be improved; Not only ensure the real-time and high safety of the leveling operation under the high temperature platform, but also avoid interference with the model during the printing process. High-Speed Printing The G5Ultra boasts desktop 3D printing speeds that reach up to 220mm/s. With regards to the flow rate of the materials, the G5 Ultra is capable of depositing a staggering 0.8kg per hour, ensuring it stands out for individuals requiring rapid production without compromising the intricacies of design or the overall quality of the final product. High-Speed Printing The G5Ultra boasts desktop 3D printing speeds that reach up to 220mm/s. With regards to the flow rate of the materials, the G5 Ultra is capable of depositing a staggering 0.8kg per hour, ensuring it stands out for individuals requiring rapid production without compromising the intricacies of design or the overall quality of the final product. Why Choose FGF Pellet 3D Printer? Reduce Costs Pellet extrusion 3D printing offers significant savings, cutting costs up to 10X compared to traditional filament-based methods. Shorten Lead Times Enjoy speeds up to 10X faster than conventional filament extrusion 3D printing, drastically reducing project lead times Excellent Material Properties Use original materials for optimal material properties, ensuring enhanced performance of printed components through superior quality. Eco-Friendly Our 3D printing innovation uses pellets and shredded recycled plastic for sustainable, eco-friendly additive manufacturing alternatives. Get a quote
- RESONANT MIXERS | POLARTEK POLIMER
Energetic Acoustic Mixser, Pharma Acoustic Mixser, Mikser, Mixser, Karıstırma, Sesle Karıstırma. ACOUSTIC MIXSERS LAB RAM I Compact and Power-Packed The LabRAM I is designed for batch mixing of developmental and repetitive mixes. With a 1.1 lb (500 gram) payload capacity and up to 100g acceleration, LabRAM I introduces a significant power increase to bench mixing that scales easily on larger ResonantAcoustic® Mixers. Key Processing Capabilities Mixing and processing any combination of Solids/Powders – from nano-scale, up Liquids/Gases Viscous/Slurry materials Coating, Milling, Grinding processes On-board control of optional processing accessories Automatic Vacuum System Manual Vacuum System RTD Temperature Monitoring Develop, store, and secure up to 100 recipes Monitor mixing parameters in real-time Download processing data for analysis LabRAM I Features Up to 1.1 lb (500 gram) payload processing capacity Integrated touch screen operating system Intense, but gentle acoustic mixing for rapid, repeatable, ultra-high quality results Fully enclosed, interlocking acoustic mix chamber Height-adjustable vessel holder accepts many vessel types Multiple level security and access control Available Processing Accessories Include Automatic Vacuum System Manual Vacuum System PHARMA RAM PHARMA RAM PHARMA LAB RAM I Simple, Powerful Processing to Triple Your Daily Revenue Resodyn’s PharmaRAM I is designed from the bench up to multiply compounding efficiency by 3-6x – every single day. Designed for high-volume, repetitive mixes, PharmaRAM I is ideal for recipe-driven functions by pharmacy technicians. With a 0.66 pound (300 gram) capacity at up to 100g acceleration, PharmaRAM I’s efficient and easy-to-use controls and functions deliver low RSD, exceptional mix quality of virtually any combination of ingredients – no other mixing technology is as versatile or as profitable. Key Processing Capabilities Mixing and processing any combination of Solids/Powders of nearly any particle size Creams and lotions Three power settings Wide selection of mixing times Eliminates cross-contamination Reduces cleaning time and supplies PharmaRAM I Features 0.66 lb (300 gram) payload processing capacity Easy operator training and use Intense, but low shear acoustic mixing causes random particle motion for consistent, exceptional quality Fully enclosed, interlocking acoustic mix chamber Height-adjustable vessel holder accepts many vessel types No operator intervention required while mixing Fast, simple clean-up OMNI RAM H OmniRAM Features Up to 11 lb (5 kg) payload processing capacity Intense, but gentle acoustic mixing for rapid, highly repeatable, ultra-high quality results All housing and enclosure materials are sealed, purged, 304L Stainless Steel Redundant ground paths mitigate static charge build-up Remote Control Panel (operation up to 2.5 miles (4 kilometers) Laptop based human machine interface (HMI) Integrated, color, touch-screen operating system Sealed, hazardous rated, SS 304 mixing platform prevents entry of mixing materials into the enclosure. Fully enclosed, interlock-able acoustic mix chamber Height-adjustable holder accepts many vessel types Multiple level security and access control Temperature sensor – 316L resistance temperature detectors (RTDs) with m12 connector (optional) THE Industry Standard – Class I Div I Class II Div I Ready Specifically designed for mixing hazardous and energetic materials, the OmniRAM H introduces significant benefits. Government and defense customers rely on ResonantAcoustic® Mixers’ technology for high quality, safe, and low-cost processing of energetic and hazardous materials. The OmniRAM H delivers better results, improved efficiency, and new product opportunities at a payload capacity that bridges LabRAM II H developmental capabilities with larger RAM H batch and continuous systems. Key Processing Capabilities Mixing and processing up to 11 lb (5 kg) of any combination of Solids/Powders – from nano-scale, up Liquids/Gases Viscous/Slurry materials Coating, Milling, Grinding Processes Concurrent Mixing and Vacuum at temperature Concurrent Vacuum and Curing at Temperature Jacketed Mixing Vessel provides optional temperature control from 302°F (150°C) heating to 0°F (-18°C) cooling On-board control of processing accessories Integrated vacuum control unit Jacketed vessel temperature control Develop, store, and secure up to 100 recipes for permanent recording of operations and measured results Monitor mixing parameters in real-time Download processing data for analysis and documentation Adaptable to Resodyn Continuous Acoustic Mixing technology Feeder Systems Continuous processing chamber stack Order of magnitude higher processing capacity Available Processing Accessories Include Hazardous Location Vacuum Pump Jacketed Vessel Temperature Control Custom Components OMNI RAM H PRODUCT RAM SERIES RAM5 RAM 5 RAM 5 Features Up to 80 lbs. (36 kg) of mix capacity in extendable 5 gallon mixing vessels Application specific mixing vessels with many options Intense, but gentle acoustic mixing for rapid, highly repeatable, ultra-high quality results The Power of RAM at Production Scale Resodyn Acoustic Mixers’ production scale mixer, the RAM 5, brings the awesome power of ResonantAcoustics® to larger scale to drastically increase productivity and expand capabilities. RAM 5 is built on flexible and universal processing options like vacuum, temperature control, and vessel specialization. Each RAM 5 configuration matches the right processing functions and exceeds the required performance beyond traditional technologies. Key Processing capabilities Mixing and processing up to 80 pounds (36 kilograms) of any combination of Solids/Powders – from nano-scale, up Liquids/Gases Viscous/Slurry materials Coating, Milling, Grinding Processes On-board control of processing accessories Automatic vacuum system Jacketed vessel temperature control Vacuum enabled chuck accepts 5 gallon, industrial mixing bucket vessel Develop, store, and secure up to 100 recipes Monitor mixing parameters in real-time Download processing data for analysis Adaptable to Resodyn Continuous Acoustic Mixing technology Feeder Systems Continuous processing chamber stack Order of magnitude higher processing capacity Digital control, programming, recording of all critical and measured functions Jacketed Mixing Vessel provides optional temperature control from 302°F (150°C) heating to 0°F (18°C) cooling Vacuum equipped Mixing Vessel option capable of applying up to 29 inHg or 10 Torr Integral hoist system for dedicated material handling of vessels and accessories (optional) Individually specified system configurations for fast implementation and high-performance results continous mıkser CONTINOUS ACOUSTIC MIXER ram energetic LabRAM II H Features Up to 2.2 pound (1,000 gram) payload processing capacity All housing and enclosure materials are sealed, purged, 304L Stainless Steel Redundant ground paths mitigate static charge build-up Remote Control Panel (operation up to 2.5 miles (4 kilometers) Laptop based human machine interface (HMI) Remote touch-screen operating system Sealed, hazardous rated, SS 304 mixing platform prevents entry of mixing materials into the enclosure. Height-adjustable holder accepts many vessel types Multiple level security and access control Temperature sensor – 316L resistance temperature detectors (RTDs) with m12 connector (optional) THE Industry Standard – Class I Div I Class II Div I Ready Resodyn Acoustic Mixers’ hazardous location development mixer, the LabRAM™ II H is specifically designed for mixing energetic materials. The LabRAM™ II H introduces significant benefits to government and defense customers who rely on ResonantAcoustic® Mixers’ technology for high quality, safe, and low-cost processing of energetic and hazardous materials. Key Processing Capabilities Mixing and processing any combination of Solids/Powders – from nano-scale and higher Liquids/Gases Viscous/Slurry materials Coating, Milling, Grinding Processes Concurrent Mixing and Vacuum at temperature Concurrent Vacuum and Curing at Temperature Jacketed Mixing Vessel provides optional temperature control from 302°F (150°C) heating to 0°F (-18°C) cooling On-board control of processing accessories Integrated vacuum control unit Jacketed vessel temperature control Develop, store, and secure up to 100 recipes for permanent recording of operations and measured results Monitor mixing parameters in real-time Download processing data for analysis and documentation Available processing accessories include: Hazardous Location Vacuum Pump (optional) Jacketed Vessel Temperature Control Custom Components PROCESSING ACCESSORIES RAM ACCESSORIES SPRAY COATING SYSTEM Effective Particle Coating and Solvent Reduction Designed to expand the LabRAM II capabilities, the Resodyn Spray Coating System mounts to the resonator plate of a LabRAM II, 2.2 lbs. (1,000 gram) capacity device. Spray system peristaltic or syringe pump options supply highly controlled stream of material to an ultrasonic nozzle, adding a spray coating feature to LabRAM II capabilities. Utilizing the existing ResonantAcoustic® Mixing (RAM) platform, the bed of dry ingredients is fluidized while the Spray System’s ultra-sonic nozzle creates a mist, coating particles without wetting, and LabRAM II’s vacuum system maintains an appropriately dry environment, drawing off unneeded solvents. Key Processing Capabilities Improve uniformity of coating and mix quality concurrently Take advantage of RAM mixer performance to coat dry powder ingredients and reduce solvent use Coats dry / powder mix ingredients in standard 16 fluid ounce mixing vessel Meters a constant and precise amount of atomized liquid for consistent and homogeneous coating Spray Coating System Features Suitable for intermittent or continuous operation Equipped with vacuum ports to assist drying Operated with a peristaltic and / or syringe pump Easy installation and operation Integrates with effective and efficient RAM mixing and vacuum technology Compatible RAM Mixers LabRAM II PharmaRAM II
- Products | Polartek Poli̇mer Araştirma Teknoloji̇leri̇ | İstanbul
Extrusion, Bi Component Extrusion, Melt Blown Extrusion, Nonwowen Extrusion, Mono Filament Extrusion, 3D printer Filament Extrusion, Acoustic Mikser, Mikser, Twin Screw Extruder, Twin Screw Food Extruder, Twin Screw Pharma and Hot Melt Extruder, Homogenizer. WHAT WE DO TSE EXTRUSION TSE EXTRUSION Bi-Tri Component Melt Spinning Line Bi-Tri Component Melt Spinning Line NON WOWEN NON WOWEN INJECTION INJECTION ACOUSTIC MIXSER ACUSTIC MIKSER 3D FILAMENT LINE 3D FILAMENT LINE COMPRESSOR COMPRESSOR 3D PELLET PRINTER 3D Pellet Printer SPECIAL MACHINE SPECIAL MACHINE
- Injection | Polartek Poli̇mer Araştirma Teknoloji̇leri̇ | İstanbul
INJECTION MOLDING MACHINE LABORATORY INJECTION PILOT INJECTION BIG TYPE INJECTION
- Extrusion | Polartek Poli̇mer Araştirma Teknoloji̇leri̇ | İstanbul
Twin Screw Extrusion, Single Screw Extrusion, Cast Film Unit, Blown Film Unit, 3D Printer Filament Line, Filter Test Machine, Gelimat Mixser, Two Stage Press, Multi Layer Extrusion LAB SCALE TWIN SCREW EXTRUDER SYSTEM TSE EXTRUDERS POLYMERS POLYMERS EXTRUDERS Micro parallel twin screw pelletizer is composed of micro twin screw extruder, micro pelletizer unit Screw elements can be combined freely according to material characteristics The shell adopts clamshell design, which is convenient for users to clean screw, especially suitable for frequent formula switching Efficient and optimized temperature control management system provides high precision temperature control Large torque servo motor drive, can provide constant torque output within the full speed range, high and low speed running free adjustment, from dozens of grams to several kilograms of capacity arbitrary use Mini twin screw extruder usd PLC intelligent control, all information on the touch screen display adjustment The granulator is driven by servomotor, providing powerful power and equipped with strong and sharp cutting tools Micro twin screw extruder is compact in shape, occupies a small area and is easy to operate FOOD TSE POLYMERS FOOD EXTRUDERS Space-saving twin-screw compact extruder Six dosing options along the process area Hinged cylinder Patented liner removal: easy to clean Screw elements can be combined individually TSE PHARMA PHARMA PHARMA TWIN SCREW EXTRUDER Small batch size Easy cleaning and handling Removable liners Fast and accurate temperature regulation Multiple feeding openings (top and side) Modular system You have a specific type of problem or need a special configuration? FORMING FUNCTIONAL MODULE FORMING FUNCTIONAL MODULE FORMING FUNCTIONAL MODULE LAB SCALE SINGLE SCREW EXTRUDER SYSTEM FEATURES The small extruder can be used with a variety of modules to complete such processes as cast film, blown film, calendering, coating, laminating and MDO stretching. Main motor used servo motor, which can provide more stable extrusion performance Advanced PLC control and mobile touch screen operation ensure system stability and improve operation convenience. Gravimetric feeder is optional. Melt pump is optional. Professionally manufactured screw and barrelleads to high processing precision and quality. Servo motor produces high precise screw speed and powerful torque. APPLICATIONS Polymer melting, plasticizing and extruding. Optimization of processing parameters Producingcast film, sheet and tube/pipe with corresponding dies. Optional melt pump or static mixing device can be used to improve plasticization effect Manual screen changer is optional to improve the purity and quality of melt. Small Machine Direction Orientor(MDO) & Casting film Machine Small Machine Direction Orientor(MDO) & Casting film Machine FEATURES It integrates casting, stretching, haul-off and winding functions. The casting roller lifting device helps to adjust die lip. Oil based heating system is adopted. Each roller is independently driven by servo motor. Adjustable gaps betweenstretching rollers to meet different technical requirements. On-line film stretching, haul-off and winding is available. Optional Mold Temperature Controller and Water Chillerare available. Optional air knife or electrostatic adsorption device help to remove the air between film and roller surface. Optional waste trimming collection device improves winding quality. Optional constant tension winding device produces smooth film and high quality. Optional pattern roller/matte roller can be used for different surface treatments. APPLICATIONS New formula development. Novel functional film preparation. Film casting performance test. Masterbatch dispersion test. Cast film stretching test. Small Extrusion Laminating Machine Small Extrusion Laminating Machine FEATURES Small Extrusion Laminating Machine all rollers are independently driven by servo motor. Small Extrusion Laminating MachineCombined with a small single screw extruder or a small twin screw extruder, then can make a set of extrusion laminating line, or you can choose a mini type extrusion laminating machine. Chrome coated and mirror polished roller with 304 stainless steel shaft guarantees reliable quality and high surface quality of film. Rollers are heated by Mold Temperature Controller and heat conduction oil to maintain uniform roller surface temperature. APPLICATIONS Film lamination for different kinds of films. Optimization of laminating parameters. Polymer film laminating performance research. New laminating formula development. Preparation and process technology research offunctional multilayer laminated film. Small Calendering Machine Small Calendering Machine FEATURES Lab Small Three-Rolls Calendering Machine can nonstandard designed, two rolls, three rolls, or four rolls is optional. Combined with a small single screw extruder or a small twin screw extruder , then can make a set of small extrusion calendering line , which can making calender sheet forming process. Three rollers are independently driven by servo motor, Linear guide rail is applied to guide the up or bottom roller for adjusting the gap between rolls. Small calender machine combined with Single Screw Extruder and sheet die, a Sheet Extrusion Line is obtained. Chrome coated and mirror polished roller with 304 stainless steel shaft guarantees reliable quality and high surface quality of film. It integrates film casting, trimming, flatting and winding. Optional touching screen can independentlycontrol this unit controllable. Optional Mold Temperature Controller and Water Cooler makes precise temperature control of the roll. Optional air knife or electrostatic adsorption device removes the air between film and roll surface. Optional trimming collection device improves winding quality. Small calender machine optional constant tension winding device produces smooth film and high quality. APLICATIONS Lab Small Three-Rolls Calendering Machine suit for new formula development. Polymer calendaring performance test. Optimization of calendaring processing parameters. Optional fatten roll/matte roll finishes different film surface treatments. Lab Small Cast Film Machine Lab Small Cast Film Machine FEATURES Small Cast Film Machine Each roller is independently driven by servo motor, combined with a small single screw extruder or a small twin screw extruder, then can make a set of small extrusion casting and coating line,can making cast film forming process. Or you can choose the mini type cast film machine. Chrome coated and mirror polished roller with 304 stainless steel shaftguarantees reliable quality and high surface quality of film. Anodized treated aluminum alloy flatten roller smoothes the film. Along with Single Screw Extruder and film casting die a Film CastingLine forms. It integrates film casting, trimming, flatting and winding. The gap between the casting roller and the die keeps variable by adjusting the height of casting roller. Optional touching screen can independentlycontrol this unit. Optional Mold Temperature Controller and Water Cooler for precise temperature control. Optional air knife or electrostatic adsorption device removes the air between film and roll surface. Optional trimming collection device improves winding quality Optional constant tension winding device producessmooth film and high quality. APPLICATIONS Small Cast Film Machine use for new formula development. Small Cast Film Machine can be used in conjunction with small single screw extruder, and small twin screw extruder. Optimization of processing parameters. Optional fatten roll/matte roll finishes different film surface treatments Lab Small Blown Film Machine Lab Small Blown Film Machine FEATURES The electrically liftedfilm frame makes it easy to lead the film and adjust the processing parameters. Equipped with retractable devicein the blown film frame for easy transport and move. Chrome coated and mirror polished roll with 304 stainless steel shaftguarantees reliable quality and high surface quality of film. A-bracketsteel ball positioning device makes it easy to adjust the inclined angle. APPLICATIONS Equipped with Single Screw Extruder anda film blowing die a Film blowing Line comes ou Film bubble cooling, pressing and curing. Take-off and winding the tubular film. New formula development. Film blowing performance test. Masterbatch dispersion performance test. Optimization of blown film processing parameters. Lab 3D Printer Filament Extrusion Lab 3D Printer Filament Extrusion FEATURES It is used for the polymer wire extrusion molding test. The development of winding neat rows. Process optimization, cost control and small-scale production. APPLICATIONS Using SIEMENS touch operation, real-time display of the running state, alarm information and system parameters. PID temperature control, the accuracy up to ±1℃. The traction unit using imported servo motor drive and is composed of the closed-loop control system with diameter measuring instrument, can quickly response to a host of speed change,which can quickly respond to the change of the speed of the extruder. Using imported servo motor drive, to ensure the tension balance, rolling smooth and tidy. Lab Rubber Extruder Machine Lab Rubber Extruder Machine FEATURES International brand variable frequency motor. Equipped with vaned side feedersimultaneously driven by the same motor. Oil heating to ensure accurate temperature control. The screw is chilled by internal cooling water channel. Optional screw designs for different materials. Durable high strength welded frame. APPLICATIONS Extrusion of universal rubber. Mixing and reactive extrusion of rubber with different ingredients. Extrusion of simple rubber profile. Rubber formula development. Optimization of rubber extrusion parameters. Small Heavy Type Two/Three - Roll Calender For Rubber Sheet Small Heavy Type Two/Three - Roll Calender For Rubber Sheet FEATURES Optimization of 3,4,5 roll. Blending of rubber/plastic and dispersion of ingredients. Plasticizing and mixing of rubber and plastics. Rubber / plastic formula development. Preparation of rubber/plastic sheet. Optional embossing roller / matt roller for different sheet surface treatments. Surface treatments for rubber/plastic sheet. Optimization of rubber calendaring parameters. APPLICATIONS Each roller is independently driven by servo motor. Chrome coated mirror roller with 304 stainless steel shaft guarantees reliable quality and excellent film appearance. Optional electric /oil heating according to different processing conditions. Optional Mold Temperature Controller ensures fine surface and axial temperature distribution. The gaps between the three rolls can be adjusted manually. Optional calendaring rolls: 3, 4, 5 or tailored. High strength aluminum alloy frame makes it light, beautiful and durable. Two Roll Mill Two Roll Mill FEATURES Each roller is independently driven by servo motor. Chrome coated mirror roll with 304 stainless steel shaft guarantees reliable quality and excellent film appearance. Auto shutdown protection cover. Optional electric/oil heating method. Optional Mold Temperature Controller ensures fine roll surface temperature distribution. The gaps between rollers can be adjusted manually with mechanical ruler as a reference. High strength aluminum alloy frame makes it light, beautiful and durable. 304 stainless steel desktop APPLICATIONS Rubber/plastic formula development. Mixing and plasticizing of rubber and plastics. Rubber mixing and vulcanization. Extrusion of conventional rubber. Preparation of rubber/plastic sheet. Surface treatment for rubber/plastic sheet Optimization of rubber milling parameters.
- 3D Pellet Printer| Polartek Poli̇mer Araştirma Teknoloji̇leri̇ | İstanbul
3D Printer, 3DPellet Printer, Granule Printer, 3D Filamet,piocreate printer INDUSTRIAL PELLET 3D PRINTER G5 Ultra Pellet 3D Printer Desktop, Built Volume: 500×500×400mm Cut your material costs by more than 60% by printing with Plastic pellets and recycled plastics instead of filament. For a wide range of applications, 3D printing with pellets and shredded recycled plastic is a financial and environmental win-win. Nozzle Temperature up to 400℃ Rapid Heating of Hot Bed up to 120℃ Screw Extruder Design Suitable for More Materials Learn More G12 Pellet 3D Printer Large Scale, Built Volume: 1200×1000×1000mm The G12 Pellet 3D Printer is a large-format pellet extrusion printer capable of printing medium-to-large format parts. Nozzle Temperature up to 450℃ Rapid Heating of Hot Bed up to 120℃ High Flow Screw Extrusion Powerful Servo Motor Learn More G40 Pellet 3D Printer Large Scale, Built Volume: 3725×2500×1330mm The G40 Pellet 3D Printer, PioCreat’s largest industrial printer, is a versatile and reliable industrial additive and CNC five-axis manufacturing integrated Machine Large Working Space Workbench Design CNC Five-axis Head High Flow Screw Extrusion Learn More What is pellet 3D printer? Fused granulate fabrication (FGF) is an Screw extrusion-based 3D printing technique where plastic pellets are fed and extruded through a nozzle. FGF may be referred to as Fused Granulate Fabrication, Fused Particle Fabrication, or Pellet 3D Printing. What is the different between FGF and FFF 3D printing? FGF and FFF 3D printing differ primarily in material use. FGF uses melted plastic pellets, offering stronger extrusion and suitability for large industrial parts, lower costs, and environmentally friendly production. FFF uses plastic filaments, which can suffer material performance loss and filament breakage. Which materials can be used with a pellet 3D printer? Pellet 3D printers offer outstanding material adaptability, supporting both traditional commercial thermoplastics and recycled materials like PLA, ABS, PETG, and TPU. Additionally, they are compatible with popular carbon fiber-reinforced materials for FGF printing, including PC-CF, PA-CF, PLA-CF, and ABS-CF. Are pellets cheaper than filament? Pellets are cheaper than filament not only because one processing step is eliminated but also because pellet-form plastics are used in injection molding and other types of manufacturing already, so the market for pellets is huge, which keeps prices low. What are the advantages of Pellet 3D printers? Pellet 3D printing reduces costs by 60–90% compared to filament, offers high extrusion volume and stable feeding for efficient, large-format printing, and allows for a wide range of thermoplastics with customizable color options during printing, ideal for industrial use. What is the extrusion volume of PioCreat pellet 3D printers? The G5Ultra offers a maximum extrusion volume of 0.8 kg/h, the G12 reaches 5 kg/h, and the G40 delivers up to 25 kg/h—significantly surpassing the 40–50 g/h extrusion volume typical of FDM 3D printers.
- BİG TYPE INJECTION | POLARTEK POLIMER
Special injection molding,Micro injection,Overmold molding,Hotmelt injection,Termoset injection,ceramic injection(PIM),Thermoplastic injection molding. BIG LINE INJECTION BOY 80 E The BOY 80 E provides 800 kN clamping force. Given the easy handling of the machine, the users of the BOY 80 E enjoy maximum flexibility. BOY 100 E Some more of everything! Greater daylight between tie bars and larger platen distances as well as a clamping force of 1000 kN characterize the BOY 100 E. BOY 125 E Significantly stronger, larger and more powerful, were the requirements for the development of BOY 125 E. 1,250 kN clamping force characterizes now the new machine upper limit at BOY.
- Extruder Extrusion| Polartek Poli̇mer Araştirma Teknoloji̇leri̇ Ti̇c.ltd.şti̇. | İstanbul
POLARTEK POLİMER ARAŞTIRMA TEKNOLOJİLERİ olarak bi component melt spinning hizmeti veriyoruz. WHAT WE DO EXTRUSION EXTRUSION LAB INJECTION LAB INJECTION Bi-Tri Component Melt Spinning Line Bi-Tri Component Melt Spinning Line NON WOWEN NON WOWEN ACOUSTIC MIXSER RESONANT MIKSER 3D FILAMENT LINE 3D FILAMENT LINE SPECIAL MACHINE SPECIAL MACHINE ULTRA SILENT DRY AIR COMPRESSOR ULTRA SILENT DRY AIR COMPRESSOR 3D PELLET PRINTER 3D PELLET PRINTER We are manufacturer and supplier of Extruder Systems , Injection Moulding Machine and Acoustic Mixers, We manufactured and sold many extruders to food, textile, polymers, academia etc. In Turkey and to many countries. We are supplier of high performance equipment for the manufacture of technical materials. We are able to supply a variety of systems in laboratory, pilot, and production scales for polymers, foods, pharma, and defence. We are distributor of FET, Fibre Extrusion Technology, is a leading supplier of state of the art process technology and equipment for the man-made yarns and fibre extrusion industry. FET offers in-depth expertise and knowhow into design, process technology, electronics, manufacturing and after sales service. FET support customers for developing of new products and for R&D departments for man-made fibre and yarn extrusion. We are represent one of leading company, BOY, for injection moulding machine. BOY injection moulding machines: Innovation in plastic processing Impressiv advantages: BOY's design concepts are; Maximum flexibility, Small footprint, Optimum production conditions, Large mould fixing dimensions, Flexible use of moulds, Intuitive use of control, Comfortable operation, Minimum electricity consumption, Low cooling capacity ,
- Special Extrusion | Polartek Poli̇mer Araştirma Teknoloji̇leri̇ | İstanbul
Lab Small Multi Layer Cast Film Machine | 2 layer| 3 layer | 5 layer Cast Film Test Line, Lab Multi Layer Blown Film Line 2 Layer, 3 Layer, 5 Layer Film Blowing Machine,Mini Type Multi Layer Co-extrusion Casting & MDO Film Line,Biaxially Oriented Film Stretching Machine-Biaxial Stretching Film Simulator,Two Roll Calendering Laminating Line,Rubber Extrusion Calendering & Laminating Line,Machine Direction Orientor MDO Machine,Torque Rheometer SPECIAL EXTRUSIONS Lab Small Multi Layer Cast Film Machine | 2 layer| 3 layer | 5 layer Cast Film Test Line Lab small multi layer cast film machine | 2 layer| 3 layer | 5 layer cast film test line FEATURES The user can select the number of small lab extruder according to the structure of the film, and combine with the double layer cast film die, three layer cast film die or five layer cast film die to form a small lab multi-layer co-extruded blown film machine. The film structure design can be divided into A/B, A/B/C, A/B/C/B/A, A/B/C/B/A, A/B/C/D/E symmetrical or asymmetric structure according to the die and numbers of small extruder. Molds can be made with an Feed Blocks or Multilayer Manifold Dies. The Feed Blocks die has a lower price, which can meet the need of sample making in conventional laboratory products. The Multilayer Manifold Dies can meet the application of higher thickness uniformity and higher layer ratio. The lab mini extruder is driven by servo motor, controlled by PLC, PID temperature setting, screw structure optimization to ensure good plasticization and stable extrusion. The roller can be manually lifted and lowered to reduce the air gap between the Die, to improve the film quality. Hard chromium - plated mirror roller with 304 stainless steel roll core, reliable quality, highly surface finish for product. The machine all driven by servo motor, to achieve smooth and precise running. Each roll of the lab small multi-layer coextruder is driven independently by servo motor, and the running is stable. The speed ratio of each roll can be adjusted freely. Advanced multi-axis synchronous technology ensures the synchronization of each roll speed. Advanced PLC control and mobile touch screen operation ensure system stability and improve operation convenience. Gravimetric feeder is optional. Melt pump is optional. On this basis, it can be derived into lab small multi-layer co-extrusion calender machine and lab small multi-layer co-extrusion film laminating machine. MDO longitudinal stretching unit can be selected to form lab small online cast film MDO stretching line. Lab Multi Layer Blown Film Line 2 Layer, 3 Layer, 5 Layer Film Blowing Machine Lab Multi Layer Blown Film Line 2 Layer, 3 Layer, 5 Layer Film Blowing Machine FEATURES The user can select the number of small lab extruder according to the structure of the multi layer blown film, and cooperate with the 2 layer blown film die, three layer blown film die or five layer blown film die to form a small lab multi-layer film blowing machine. The film structure design can be divided into A/B, A/B/C, A/B/C/B/A, A/B/C/B/A, A/B/C/D/E symmetrical or asymmetric structure according to the die and numbers of small extruder. The multi layer blown film die includes sleeve type, planar superposition type, subuliform superposition type etc. Among them, planar superposition die is suitable for materials with large temperature difference and sensitive to temperature because it can be divided into sections for temperature control. The lab small extruder is driven by servo motor, controlled by PLC, PID temperature setting, screw structure optimization to ensure good plasticization and stable extrusion. Motorized height adjustment film tower, convenient to lead film and process adjustment. Hard chromium - plated mirror roller with 304 stainless steel roll core, reliable quality, highly surface finish for product. Film bubble stabilizing cage and synchronous adjustable film collapsing frames with polished teak wood or guide roller. The machine all driven by servo motor, to achieve smooth and precise running. Each roll of the lab small multi-layer blown film line is driven independently by servo motor, and the running is stable. The speed ratio of each roll can be adjusted freely. Advanced multi-axis synchronous technology ensures the synchronization of each roll speed. Advanced PLC control and mobile touch screen operation ensure system stability and improve operation convenience. Gravimetric feeder is optional. Melt pump is optional. Refering: Lab small multi layer blown film line, small multi layer film blowing line, lab multi layer co extrusion film blowing machine, small multi layer co extrusion blown film machine. Mini Type Multi Layer Co-extrusion Casting & MDO Film Line Mini Type Multi Layer Co-extrusion Casting & MDO Film Line FEATURES Both extruders are controlled by the main touch screen controller for remote control. Preparation of single or multi layer casting film. Preparation of coating film. Preparation of machine direction orientor(MDO) with multilayer co-extrusion cast film. Optional melt pump and static mixer can improve plasticization and film quality. Optional Mold Temperature Controller and Water Cooling device is available for temperature control. Optional air knife or electrostatic adsorption device can improve the film adsorption & cooling. Optional waste film trimming collection device improves winding quality. Optional constant tension winding device producesf smooth film and high quality. Optional pattern roller/matte roller can be used for different surface treatments. Feature and size is customizable. A PPLICATIONS Preparation of multilayer functional film. Polymer casting performance test. Polymer MDO performance test. New formula development. Optimization of processing parameters. Small scale preparation of narrow film. Laboratory Multi Layer Co-extrusion Coating & Casting & Laminating & MDO Line Laboratory Multi Layer Co-extrusion Coating & Casting & Laminating & MDO Line FEATURES Both extruders are controlled by the main touch screen controllerfor remote control. Preparation of single layer cast film. Preparation of multilayer co-extrusion cast film. Preparation of machine direction orientor(MDO) with multilayer co-extrusion cast film. Optional melt pump and static mixer can improve plasticization and film quality. Optional Mold Temperature Controller and Water Cooling device is available for temperature control. Optional air knife or electrostatic adsorption device can improve the film adsorption & cooling. Optional waste trimming collection device improves winding quality. Optional constant tension winding device producesf smooth film and high quality. Optional pattern roller/matte roller can be used for different surface treatments. Feature and size is customizable. APPLICATIONS Preparation of multilayer functional film. Polymer casting performance test. Polymer MDO performance test. New formula development. Optimization of processing parameters. Small scale preparation of narrow film. Biaxially Oriented Film Stretching Machine-Biaxial Stretching Film Simulator Biaxially Oriented Film Stretching Machine-Biaxial Stretching Film Simulator FEATURES Including biaxial stretching mechanism, static pressure box, heating oven High-performance temperature sensor Servo motor drive Real-time monitoring of polymer materials, tensile changes in the film APPLICATIONS Prepare Biaxially oriented film samples for properties test and optimization of formulations. Evaluate the biaxial orientation capability of new materials and films in lab-scale. Biaxial tensile properties of polymer film. Investigate biaxial orientation temperatures, ratios, speeds for production scale up. Two Roll Calendering Laminating Line Two Roll Calendering Laminating Line FEATURES The rollers are independently driven by servo motorsfor flexible speed control. Chrome coated mirror roller with 304 stainless steel shaft guarantees reliable quality and excellent film appearance. Roller's number is optional, 2/3/4/5 rollers are acceptable. Optional Mold Temperature Controller and Water Cooling makea uniform temperature distribution on roll surface. Optional trimming waste collection device improves sheet quality. Optional constant tension winding device producessmooth film and high quality. Optional pattern/matte roller can be used for different surface treatments. Optional hydraulic or air cylinder for different materials. Optional two / three / four rollers configurationfor different processing technology. APPLICATIONS Calendering and laminating is available Preparation of different sheet. New formula development. High viscosity polymer calendaring. Preparation ofmulti-functional polymer composite sheet. Rubber Extrusion Calendering & Laminating Line Rubber Extrusion Calendering & Laminating Line FEATURES Each roller is independently driven by servo motor, ensuring precise roller revolution speed and speed ratio between adjacent rollers. Chrome coated and mirror polished roller with 304 stainless steel shaft guarantees reliable quality and high surface quality of film. Optional melt pump and static mixer can improve plasticization effect and film homogenization. Optional Mold Temperature Controller and Water Cooling device. Optional trimming collection device improves winding quality. Optional Constant Tension Device makes smooth winding effect and steady subsequent machine direction tensile. APPLICATIONS Preparation of different sheet. New formula development. High viscosity polymer calendaring. Preparation ofmulti-functional polymer composite sheet. Machine Direction Orientor MDO Machine Pilot Line Machine Direction Orientor MDO Machine Pilot Line FEATURES The horizontal structure is easy to expand and convenient to thread the film, more suitable for pilot and small-scale production. Preheat roller, stretching roller, annealing roller and cooling roller are independently driven by servo motor, with higher speed control accuracy. Stretch roller gap adjustable, can achieve "zero pitch" stretch, reduce necking effect. Single, double (or even multi-point) stretch optional, adjustable stretch ratio. Oil / electric heating optional: oil heating. Temperature uniformity, and electric heating can obtain higher process temperature. High-performance PLC with 10-inch touch screen, high control accuracy, more convenient operation. Horizontal or vertical configuration optional APPLICATIONS Machine Direction tensile membrane laboratory preparation and pilot-scale production. Study and optimization of machine direction stretching production process. Tensile testing of films. R&D of new film materials and ln-line machine direction stretching combined with extrusion casting test lines. Machine Direction Orientor MDO Machine Machine Direction Orientor MDO Machine FEATURES MDO machine can use as an offline stretching film machine, or combined with small single screw extruder, small twin screw extruder, small triple screw extruder, and a small cast film machine, to form a MDO on-line cast film stretching machine. Or you can choose the MDO casting integrated machine. Rollers for preheating, stretching, annealing and cooling are all independently driven by servo motors. The gaps between the rollers can be adjustedby moving the relevant roll horizontally. Mold Temperature Controller and heat conduction oil is adopted to heat the rollers. 10’ touch screen controlleris easy to operate. European standard aluminum alloy frame makes it light, strong, corrosion resistant and durable. 304 stainless steel desktop, practical and beautiful. Single or multi stage draw sections. Size customizable APPLICATIONS Off-line film machine directionorientation. Optional single-point or two-point machine direction orientation. Combined with Mini Precise Film Casting Line an on-line MDO line is made up. Preparation ofstretching film with different draw ratio. New formula development. Functional film preparation and processing research. Filmtensile performance test. Optimization of film stretching parameters. Triple Screw Die Face Cutting Triple Screw Die Face Cutting Granulation Line Use For Ceramic Phone Backboard FEATURES In order to meet the application requirements of the high fill ratio of zirconia ceramics, the triple screw die face cutting granulation line is specially upgraded as follows Triple screw extruder has better dispersing effect and staying time than twin screw extruder and is especially suitable for the blending extrusion of high filling master batch. In order to meet the application demand of high filling zirconia ceramic powder, the extruder adopts ultra-high torque drive system The optimized combination of screw elements can improve the plasticization and homogenization effect and ensure the high fluidity of filling inorganic material Both the screw element and the barrel lining are made of imported advanced alloy steel, and the wear resistance is improved significantly, which is half of the time than common steel. Specially optimized heating and cooling system ensures material temperature control and product performance Driven by a high power motor, the cutting head provides strong power and is equipped with a strong and sharp cutting tool, which is especially suitable for hard ceramic particles PPTC Resettable Fuse Sheet Extrusion Line PPTC Resettable Fuse Sheet Extrusion Line FEATURES The rollers are independently driven by servo motor, sfor flexible speed control. Chrome coated mirror roller with 304 stainless steel shaft guarantees reliable quality and excellent film appearance. The roller are specially strengthened to cope with the high hardness of the sheet. APPLICATIONS This euqipment is made for PPTC resettable fuse sheet. Preparation of different sheet, and laminating sheet, as ABA/ABC structures. New formula development & pilot manufacture. High high filler polymer calendaring. Preparation of multi-functional polymer composite sheet. Filter Pressure Value (FPV) Tester Filter Pressure Value (FPV) Tester FEATURES The melt pump is driven by servo motor. Equipped with manual plate nitride treated screen changer of high hardness and wear resistance. High precise melt pressure sensor provides an accurate melt pressure. The extruder can be moved axially along the linear guide rail on the top of the frame. APPLICATIONS Accurate measurement of melt volume flow rate. Accurate melt conveying. Accurate pressure measurement before and after the melt pump Masterbatch dispersion test. Quality inspection and control during film production. Pigment quality inspection and control. Torque Rheometer Torque Rheometer FUNCTION It provides power for other modules to extract data from temperature, pressure and torque, and then calculates and graphically. It can connect torque module, capillary module, single/twin/triple screw extruder module, casting module, calendering module etc.. FEATURES Driven by high precision servo motor. Controlled by advanced OPC technology and manipulated viaan independent computer. Remote/local multi-point control is available for each independent unit. Labview® based data analysis program with powerful functions and user-friendly interface. APPLICATIONS Operation and control platform forpolymer rheo-station to control other modules. Providedriving, measurement and control function for the other modules.
- PILOT INJECTION | POLARTEK POLIMER
PILOT LINE INJECTION BOY 35 E The BOY 35 E is a four-tie bar, fully hydraulic reciprocating screw injection moulding machine with two-platen clamping unit and swivel-out injection unit. BOY 50 E As entry-level model with 500 kN clamping force, the BOY 50 E includes a multitude of functions already in standard execution. BOY 60 E With its appealing design, the BOY 60 E is an optical highlight. But it is more than just optics which convinces the experts, namely its technical and operational values and its orientation towards cost-saving.
- Product Map | Polartek Poli̇mer Araştirma Teknoloji̇leri̇ | İstanbul
Extrusion, Bi Component Extrusion, Melt Blown Extrusion, Nonwowen Extrusion, Mono Filament Extrusion, 3D printer Filament Extrusion, Acoustic Mikser, Mikser, Twin Screw Extruder, Twin Screw Food Extruder, Twin Screw Pharma and Hot Melt Extruder, Homogenizer. Bi-Tri Component Melt Spinning Line Bi-Tri Component Melt Spinning Line NON WOWEN NON WOWEN INJECTION INJECTION ACOUSTIC MIXSER ACOUSTIC MIKSER 3D FILAMENT LINE 3D FILAMENT LINE SPECIAL MACHINE SPECIAL MACHINE COMPRESSOR COMPRESSOR PELLET PRINTER GAZ LINE EXTRUSION EXTRUSION UNIT TWIN SCREW EXTRUSION POLYMER FOOD PHARMA SINGLE SCREW EXTRUSION BLOWN FILM UNIT CAST FILM 3D FILAMENT FORMING FUNCIONAL MODULE RUBBER SPECIAL EXTRUSION Lab Multi Layer Cast Film Machine | 2 layer| 3 layer | 5 Layer Cast Film Test Line Lab Multi Layer Blown Film Line | 2 Layer| 3 Layer | 5 Layer Film Blowing Machine Mini Type Multi Layer Co-extrusion Casting & MDO Film Line Laboratory Multi Layer Co-extrusion Coating & Casting & Laminating & MDO Line Biaxially Oriented Film Stretching Machine-Biaxial Stretching Film Simulator Two Roll Calendering Laminating Line Machine Direction Orientor MDO Machine Lab Line Filter Pressure Value (FPV) Tester Triple Screw Extruder Module Torque Rheometer PPTC Resettable Fuse Sheet Extrusion Line Machine Direction Orientor MDO Machine Pilot Line Rubber Extrusion Calendering & Laminating Line EXTRUSION PRODUCTION LINE Aluminum Plastic Film Production Line For Lithium Ion Battery Conical Single Screw Extrution Granulation Line For Crushing PET 3D Printer Filament Machine Single Screw Extrusion Small Hollow Pipe Line Disposable Surgical Mask Production Line_Face Mask Making Machine BI-TRI COMPONENT MELT SPINING LINE FET 100 SERIES Laboratory and Pilot Systems Bi & Tri – Component Melt Spinning Technology FET 200 Series Wet Spining Line Monofilament Extrusion Lines Multifilament Extrusion Lines Melt Spinning Systems For Non-Woven Structures Wet Spining Lab Line INJECTION UNIT LAB - XXS LAB- XS LAB 22E PRO 80 E 35 E 50 E 60 E 125 E 100 E ACUSTIC MIKSER LAB RAM I LAB RAM II OMNI RAM CONTINOUS ACOUSTIC MIXSER (CAM) PHARMA OMNI RAM PHARMA CONTINOUS ACOUSTIC MIXSER (CAM) PHARMA RAM I PHARMA RAM II RAM 5 RAM 55 PHARMA RAM 5 PHARMA RAM 55 ENERGETICS AND HAZARDOUS MATERIAL MIXERS LAB RAM II H OMNI RAM H CONTINOUS ACOUSTIC MIXSER H (CAM) RAM 5 H RAM 55 H RAM ACCESSORIES PELLET PRINTER PELLET PRINTER G5 ULTRA G12 G40